Some Quick Tips on Maintenance and Leadership for Junior Officers
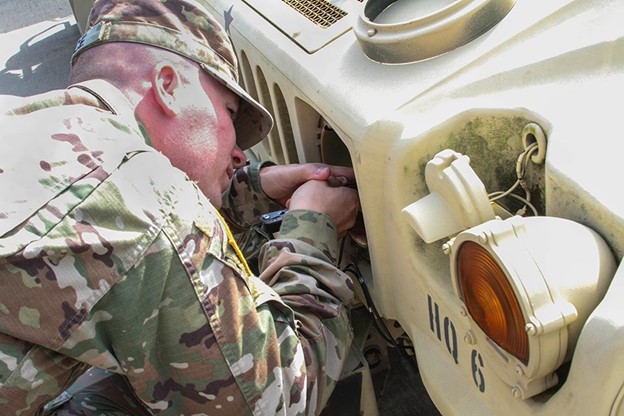
Maintenance – an important topic that isn’t taught very well at most commissioning sources or BOLCs. For many Lieutenants, maintenance is learned “on the job”. If you’re lucky, you have NCOs or fellow officers who assist in the process. If you’re REALLY lucky, you have a high-speed Warrant Officer who not only runs a tight ship but is willing to help teach young LTs and CPTs a little bit about what he/she knows. But many young officers aren’t so lucky. In fact, I’ve served with more than a few Majors and Lieutenant Colonels who didn’t know what a 5988E or a 2404 were, didn’t know where their BII was stored in their HMMWVs or LMTVs, couldn’t tell you where the grounding rods for their generators were, what items need to be in the Equipment Record Folder, and had no clue what PS Magazine was.
This isn’t as uncommon as you might think. “Motor Pool Monday” isn’t always a priority. There are a lot of things young leaders must oversee. And it’s easy to focus on the high visibility tasks or jobs that come easily – especially if you have NCOs or others who are telling you “I got this” in the areas you don’t have knowledge in or are less exciting to you personally. That said, maintenance is a critical (although often not sexy) part of Army operations. I firmly believe that maintenance also provides an opportunity for junior officers to develop and exercise their leadership abilities.
With that in mind, I wanted to share a few tips on maintenance that were shared with me over the years. My hope is that they may help you (if not now, perhaps later) improve your organization’s ability to conduct effective maintenance operations and hopefully help you develop as a leader.
- Review any inspection checklists associated with maintenance for your organization. Understand not only where your program was lacking during the last inspection, but make sure you understand all of the items and terms on the checklists! This can be tough – have the humility to ask for help from those with more knowledge on the topic (but also do your homework – the internet is a wonderful thing).
- Have a weekly class (help before motor stables begins) designed to increase knowledge of a specific topic – PS magazine might give you some ideas. Put it on the training schedule. Assign a different person to plan and lead each session. Make sure they rehearse it before giving it to the platoon/company. Make sure you teach one of these and don’t just assign them to others.
- Spend time in the motor pool. Meet with NCOs and/or Warrant Officers working there on their turf. Many officers “lead by walking around” but you’d be surprised how many don’t make it to the motorpool. Use this time to learn about your people – and ask questions about the equipment you’re unfamiliar with. In my experience, mechanics love to share their knowledge.
- Be present at motor stables. You can’t tell others to focus on maintenance if you don’t. Lead by example. This starts with being physically present – and doing more than watching others do the work. That leads to item #5.
- Spot check 5988Es. Are they being filled out correctly? If they aren’t, maybe you need to plan a class on how to do them correctly
- Go through your vehicles and equipment. Is there trash left in the vehicles? Is something not set up properly? Point out issues. Let people know you’re paying attention.
- Are BII boxes locked? If so, are the keys in the motor pool during motor stables so you can unlock the boxes and examine the items?
- Hide “Reward” cards in equipment. These are note cards with instructions on them to turn the card in if found (with an expiration date). If someone is doing a proper PMCS, they’ll find the card. Turning it in gets them whatever reward you’ve agreed on with the appropriate leadership.
- Walk the line at the end of the week and check in with maintenance POCs. Were required tasks completed or are people putting it off until the next motor stables? Consider adding a maintenance check to the list of things you examine before releasing people for the weekend.
- Weapons, communication equipment, NBC gear and tools are part of maintenance – it’s not just aircraft, vehicles, trailers, and generators!
The above are just a few tips that I hope prove helpful – or at least get you thinking about maintenance (it is by no means intended to be comprehensive!). A key thing to understand is that maintenance is not “NCO business” or “Warrant Officer business”; maintenance is “leader business.” Lieutenants often get a bit of a pass on what they’re expected to know. Use this opportunity to learn and grow. If you’re a Captain who didn’t get exposed to a strong maintenance program when you were young, don’t shy away from learning about maintenance. You might become a Battalion XO someday – you don’t want to have your lack of knowledge become apparent then (it’s not pretty). If you’d like to learn more, you may want to listen to our podcast on command maintenance.
———
Jordon Swain is an active duty Lieutenant Colonel and the Director of the Center for Junior Officers. He holds a Ph.D. in Organizations and Management from Yale University and a MBA from the Wharton School. LTC Swain was mentored by some great NCOs, Warrant Officers and Officers in the realm of maintenance and hasn’t quite forgotten all of the lessons they taught him.
Related Posts
Fighting as an Enabler Leader
(U.S. Army Photo by Cpl. Tomarius Roberts, courtesy of DVIDS)Enablers provide capabilities to commanders that they either do not have on their own or do not have in sufficient quantity …
Defeating the Drone – From JMRC’s “Skynet Platoon”
If you can be seen, you can be killed—and a $7 drone might be all it takes. JMRC’s Skynet Platoon discuss their TTPs to defeat the drone.
3 Deployments Before Captain: Reflections From Down Range
Deployments challenge junior officers beyond their primary duties, often demanding adaptability, wellness management, proactive leadership, and moral integrity maintenance.